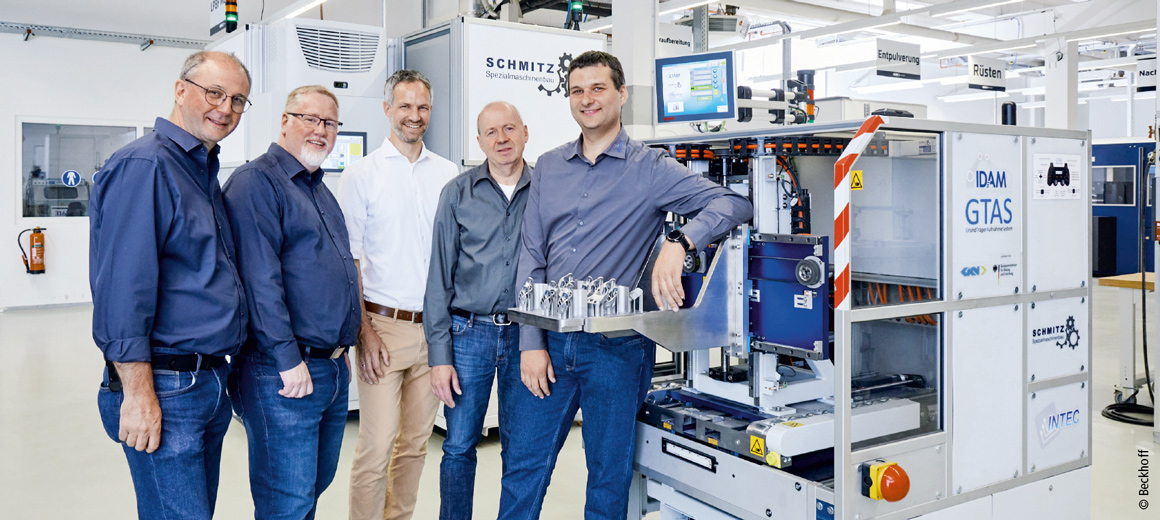
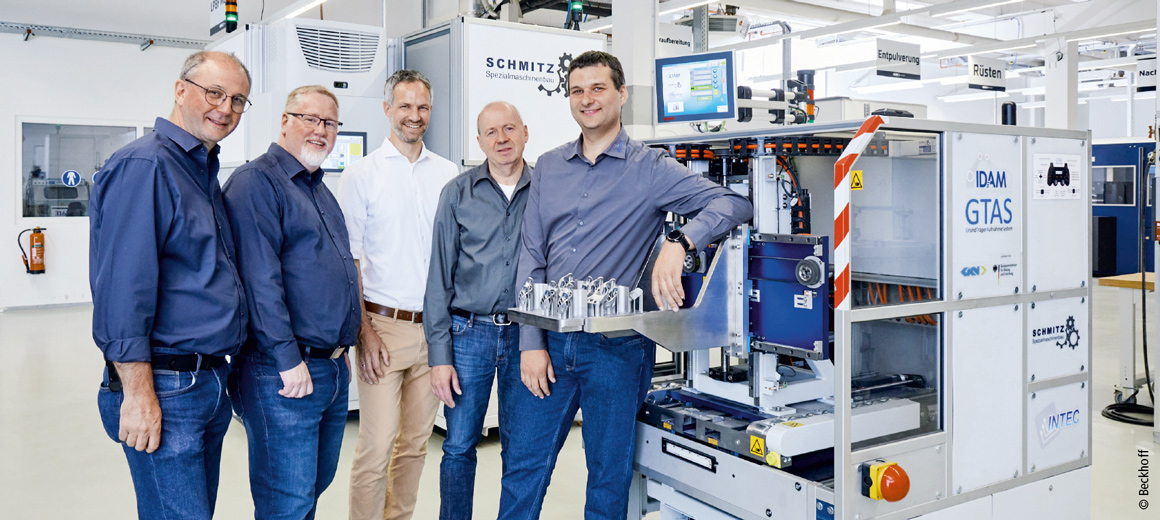
基于 PC 的控制技术助力实现 3D 打印过程中容器搬运的自动化
由德国联邦教育和研究部(BMBF)资助的 IDAM 项目旨在推动增材制造技术在汽车量产中的应用和普及。该项目的核心部件是基础载体支撑系统(BCSS),它由 Intec 和 Schmitz Spezialmaschinenbau 公司采用倍福基于 PC 的控制技术实现自动化。BCSS 的引入使得位于波恩的汽车供应商 GKN Additive 就能够将各个生产环节无缝衔接起来,打造一个金属 3D 打印批量生成全自动试点系统。
诸如激光粉末床熔融(LPBF)等成熟的增材制造技术已经适合于大批量生产,但目前仍只能作为单独的工站运行。 其中一个原因是设备的作业空间必须保持密闭。 这是因为增材制造中使用的金属粉末非常细,存在吸入风险。因此,金属粉末和零部件的进料和出料主要依赖于密闭容器进行,且这一过程大多需要手动完成。“我们的基载支撑系统成功解决了这一难题,并实现了全自动化的工艺链。”GKN Additive 的技术与工业化部门负责人 Simon Höges 博士在谈及该研究项目的潜力时自豪地说道。
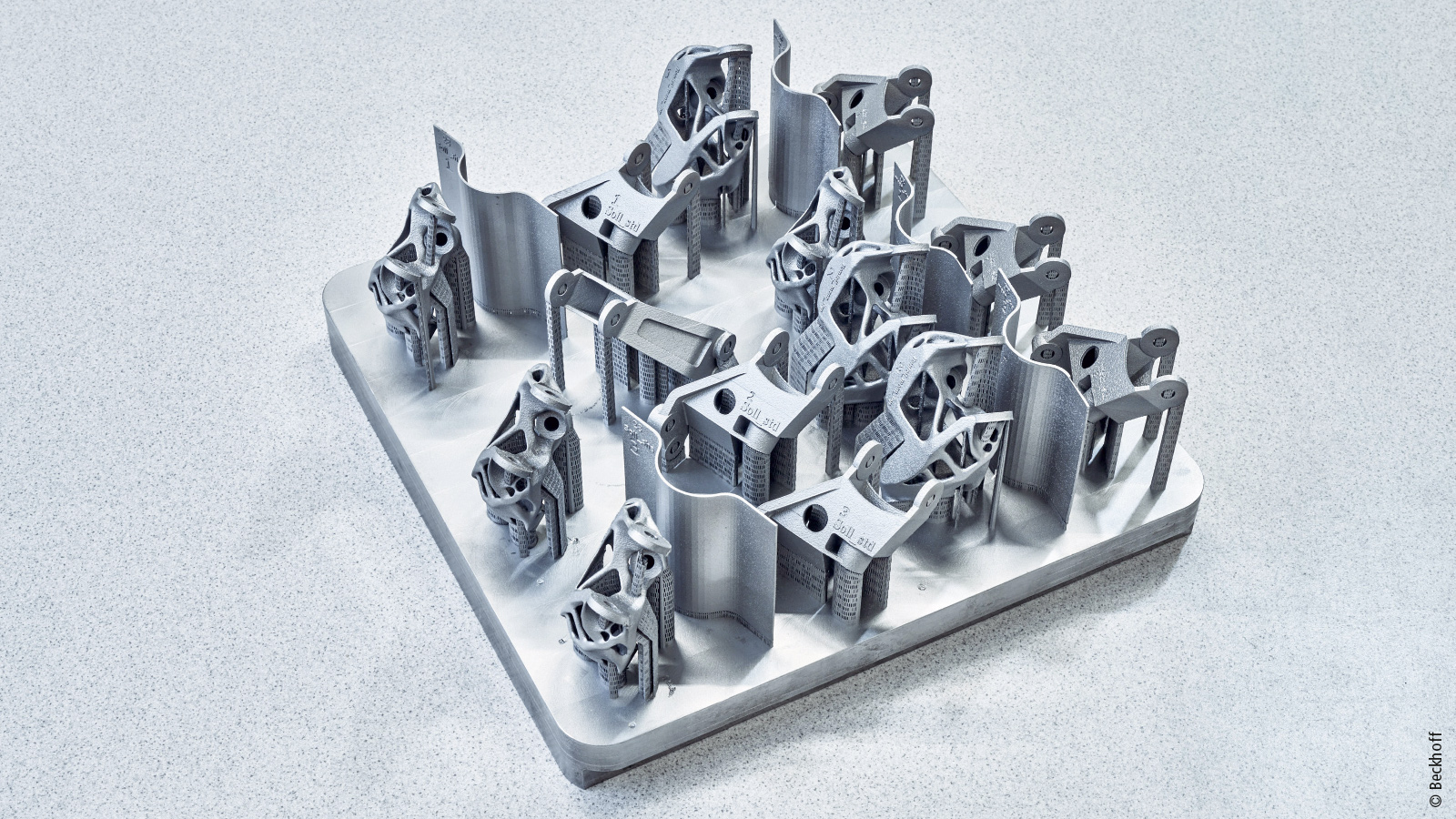
该公司已经将 LPBF 等先进的增材制造技术应用于汽车行业,并稳定生产了一段时间,制造出一系列高品质的汽车零部件。 在此过程中,金属粉末在激光束的作用下逐层熔化,制作复杂结构的零部件。其优势在于摆脱了对传统的专用工具的依赖,并且能够灵活实现各种新设计。“因此,我们目前正积极扩大生产规模,以实现批量生产。”Simon Höges 博士说道。
“BCSS 是实现增材制造工业化过程中不可或缺的一环,尤其是在推动工艺的模块化和优化资源利用方面。”Schmitz Spezialmaschinenbau 公司总经理 Reinhard Schmitz 强调道。 BCSS 可以高效地连接各个工艺步骤和设备,包括 3D 打印机、粉末处理和后处理,构建一个完整的自动化生产系统。“采用众多不同制造商的设备,不可避免地会导致出现多种不同的机械和电气接口。”Reinhard Schmitz 在解释 BCSS 在机械设计和自动化方面遇到的挑战时说道。例如,在设计基载支撑系统时,必须确保系统能够安全、精确地操控多种负载,比如直径为 330 mm 的圆柱形容器和底板,以及重达 750 kg 的矩形底板和容器。 BCSS 的总重量为 1500 kg,尺寸为 1200 x 800 mm,高度最高为 1800 mm,因此能够与来自不同供应商的自动导引运输车(AGV)结合使用,并能够灵活移动到各种系统模块中。
紧凑型驱动技术节省宝贵的安装空间
这些严格的要求对控制柜及其内部所用组件的布局和可用空间产生了极大的影响。“控制器必须尽可能小巧、轻便且功能强大,确保在提供卓越性能的同时,无需依赖空调进行散热。”Intec 公司总经理 Achim Heimermann 强调道。高性能计算机、6 个用于定位 BCSS 的轴、5 个承担传输/控制功能的轴以及各个传感器的 I/O 接口集成在一个极小的空间内,包括 外形紧凑的 AM8112 同步伺服电机和带 STO 功能的 EtherCAT 伺服电机端子模块 EL7211,以及 C6030 超紧凑型工业 PC。“工业 PC、外形紧凑的伺服电机端子模块以及单电缆式技术(OCT)帮助 Intec 节省了大量空间。”倍福蒙海姆销售办事处负责人 Wilm Schadach 表示。“如果采用其他制造商的系统,我们绝对无法达到当前这种既紧凑又简便的安装与连接效果。”Intec 公司的另一位总经理 Erik Heimermann 也证实了这一点。
这为总共三个容量为 105 Ah 的充电电池预留了充足的空间,这些能量可以确保生产线在周末期间能够自给自足地持续运行,GKN 公司计划在未来将它与 AGV 小车结合使用。“目前,BCSS 系统主要依赖电动托盘车手动粗略定位在各个工站前。”Simon Höges 博士说道。随后将启动全自动流程,第一个步骤是使用四个可调支脚对车间地面进行找平。“倍福驱动器集成了安全扭矩监控功能,对于确保各个模块间的精确对齐和定位起着至关重要的作用。”Intec 公司项目经理 Stefan Hornberger 强调道。通过集成了两个三轴加速度计的 EtherCAT 端子盒 EP3752 对可调支脚的扭矩进行监测,以检查在对齐操作后,所有支脚是否都已稳固地放置于地板上,并检测四个驱动器是否各自沿对角线方向均匀地施加相同的扭矩。只有这样,才能确保 BCSS 水平且稳固的状态,抓手便可以安全地移动到指定的高度,并按照既定的顺序开始传输容器和基板。
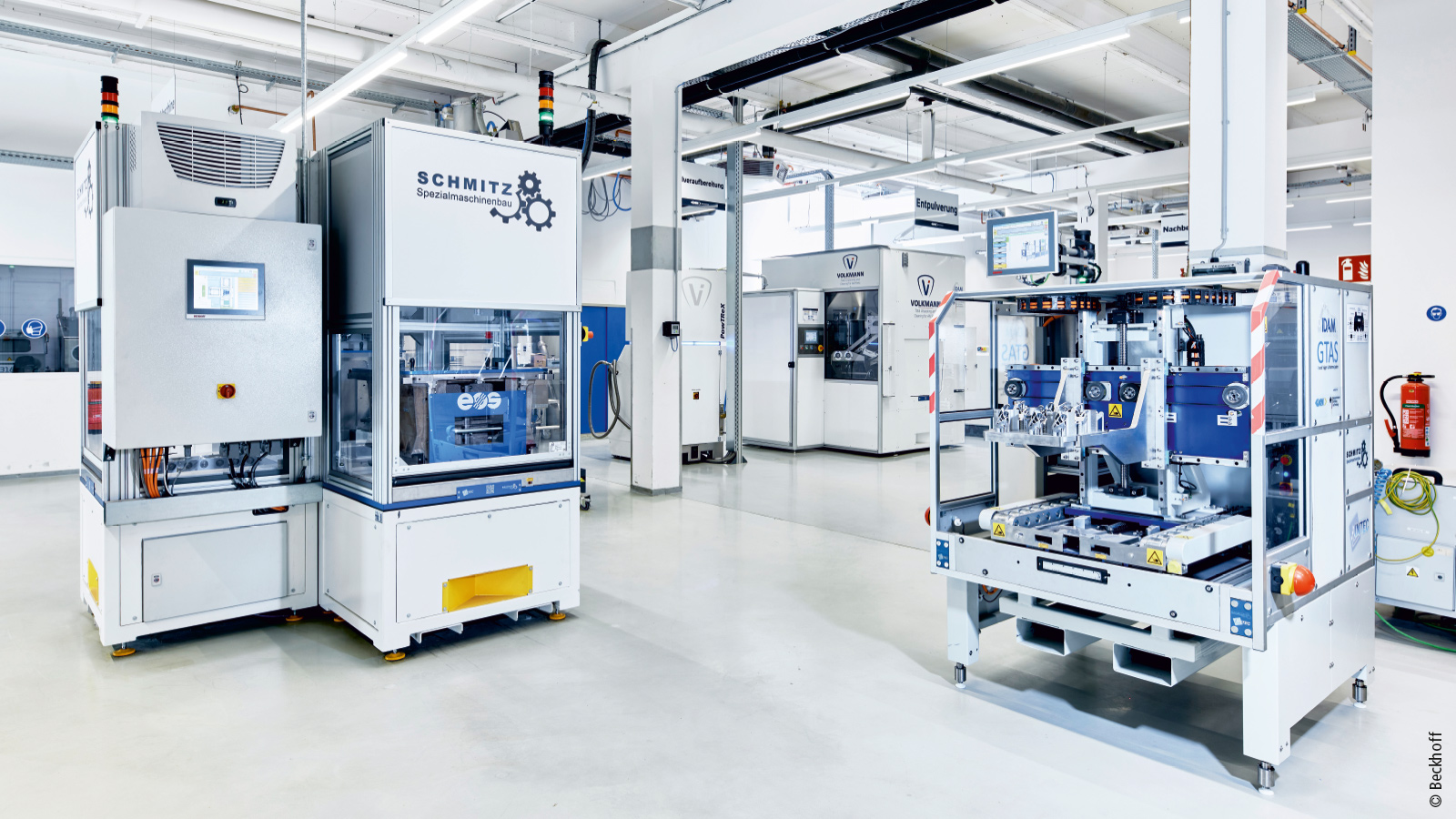
基于 PC 的控制技术具有开放性和灵活性优势
借助倍福的紧凑型驱动技术,BCSS 能够对模块前的位置偏差进行实时补偿。“高度偏移量、横向偏移量、倾斜偏移量以及角度偏移量的精度都被控制在 0.5 至 1 mm 之间。”Reinhard Schmitz 说道。为了满足这种精度要求,必须使用各种传感器。这些传感器中的数据通过 IO-Link 端子模块 EL6224 读取。两个高精度的激光传感器通过 EtherCAT 连接,用于测定 BCSS 与设备模块之间的角度偏差。“Intec 能够利用 EtherCAT 读取激光器的 XML 描述文件,并在 TwinCAT 中直接访问激光器的所有参数和数据。”Wilm Schadach 说道,这一能力充分体现了基于 PC 的控制技术的良好开放性。同时,系统还会使用相机和 TwinCAT Vision 扫描每个设备模块上的二维码,以检查底板是否已准确无误地放置在预定的模块前并确保定位精准。为了辅助电动托盘车的操作人员,BCSS 控制面板(CP3912)上会显示来自相机的实时图像。考虑到当前的安装布局,还需要使用 EtherCAT 端子模块 EL2502 及其 PWM 输出来精确控相机光源。“基于 PC 的控制技术具有灵活的集成性,能够将各种 I/O、高性能的开放式控制器、可视化组件、紧凑高效的驱动技术、机器视觉、安全和通信等功能无缝集成在同一个系统中,极大地简化了各项功能的实现过程。”Stefan Hornberger 说道。
通过集成无线手柄来设置运动指令的创新应用再一次证明了基于 PC 的控制技术无与伦比的开放性:Intec 采用 .NET、TwinCAT HMI 和 TwinCAT ADS 将无线手柄的通信数据读入系统控制中,使得操作人员与执行的动作之间的连接变得更加紧密。然后在控制面板上进一步配置容器传输过程。
在自动模式下,系统会根据定位后获取的距离信息自动调整传输周期,并随即启动相应的流程。各种系统模块以及 BCSS 的网络连接由一个中央监控单元(数字量自动化级)控制。它通过无线局域网启动传输和控制顺序,并监控流程顺序。这种更高级别的流程协调工作通过一台 C6025 超紧凑型工业 PC 完成,它通过 EtherCAT、OPC UA 或 HTTPS 汇集生产线上所有模块的生产数据。Simon Höges 博士表示:“Intec 还成功实现了与我们生产规划软件的通信,因此能够在周末期间全自动处理多个生产订单。”