

基于 PC 的控制技术助力实现大型塑料零部件增材制造
3D 打印工艺已经成为实现塑料零部件开发、原型制作和单件小批量生产创新的关键,但精度、速度和物体尺寸会对 3D 打印造成限制。波兰设备制造商 ATMAT 使用倍福的控制和驱动技术突破了这些限制。
大约还在 10 多年前,3D 打印技术主要用于快速原型开发。但如今,3D 打印已逐渐成为批量生产的一部分。位于克拉科夫的设备制造商 ATMAT 很早就认识到了 3D 打印的巨大潜力,并且在传统机械工程的基础上,专门制造工业级 3D 打印机,作为公司的第二大主力产品。ATMAT 公司目前通过新推出的 Saturn 和 Jupiter 大型打印机系列产品,在不牺牲精度、打印速度和操作便利性的情况下,将 3D 打印机的工作空间扩大到一个新的水平。开发人员基于 PC 控制技术实现了这一目标,即采用 TwinCAT 3 软件、适合控制柜安装的“经济型”面板型 PC CP6700 以及 EtherCAT I/O 端子模块和倍福的伺服驱动技术。

大幅面 3D 打印机已经涉及了汽车、航空等很多有趣的应用领域。例如,其中一个特别的项目是修复一架法国在二战前研制的老式战斗机 Caudron CR.714。不仅机身在战争中受到严重损坏,飞机还缺少螺旋桨叶片、轮毂、螺旋桨盖和电机外壳。这意味着使用传统方法重建飞机将需要花费大量的时间和成本。因此决定在 ATMAT 的支持下使用 3D 打印技术生产这些零部件。“该项目最重要的方面,同时也是最大的挑战,包括尽可能精确地再现机身形状和实际尺寸。”ATMAT 自动化部门负责人 Robert Grolik 解释道。“考虑到我们要修复的是一件博物馆藏品,我们还必须规定好如何固化打印好的零部件,以确保在组装时不会破坏历史元素。”
高精度打印尺寸达 1.2 立方米的精细零部件
这类修复的前提是高精度的 3D 打印机有足够大的工作空间,才能生产超大尺寸的飞机零部件以及复杂的几何形状。所有零部件都采用 FFF/FDM(熔融沉积成型技术)打印。在这个过程中,一台挤出机用于加热打印材料,直至熔化,送入打印头,并精确地层层堆积在工作台上,直至整个零部件打印完成。在此期间,工作台用作 Z 轴,而定时皮带传动的龙门轴则用作 X 和 Y 轴。一台 Saturn 3D 打印机被用于重建飞机零部件。它的工作空间为 1200 x 1000 x 1000 毫米,是 ATMAT 继 Jupiter 之后制造的第二款 XXL 超大幅面 3D 打印机。“我们从一开始就同等重视客户的特定项目和 3D 打印机本身。我们在紧凑型 3D 打印机方面积累了丰富的专业知识,在此基础上,我们开发出了高效率的大幅面 3D 打印机,比如 Jupiter 和 Saturn 型号。”Robert Grolik 强调说道。
Jupiter 和 Saturn 不仅适用于制作功能性原型。系统设计使得它可以直接集成到生产线上,从而优化 3D 打印单件小批量生产。“跨国公司,尤其是汽车整车制造企业,会很高兴能够利用这一优势。”Robert Grolik 解释道。原因就是:除了众多的设备选项之外,车辆个性化定制也越来越重要。“增材制造技术可以助力实现这些个性化设备选项的生产:制作时间短、方式简单且成本也低。”不仅可以打印像轮毂盖或方向盘元件这类简单的零部件;现在还可以打印体积更大、形状更复杂的结构体,包括仪表盘和照明元件。
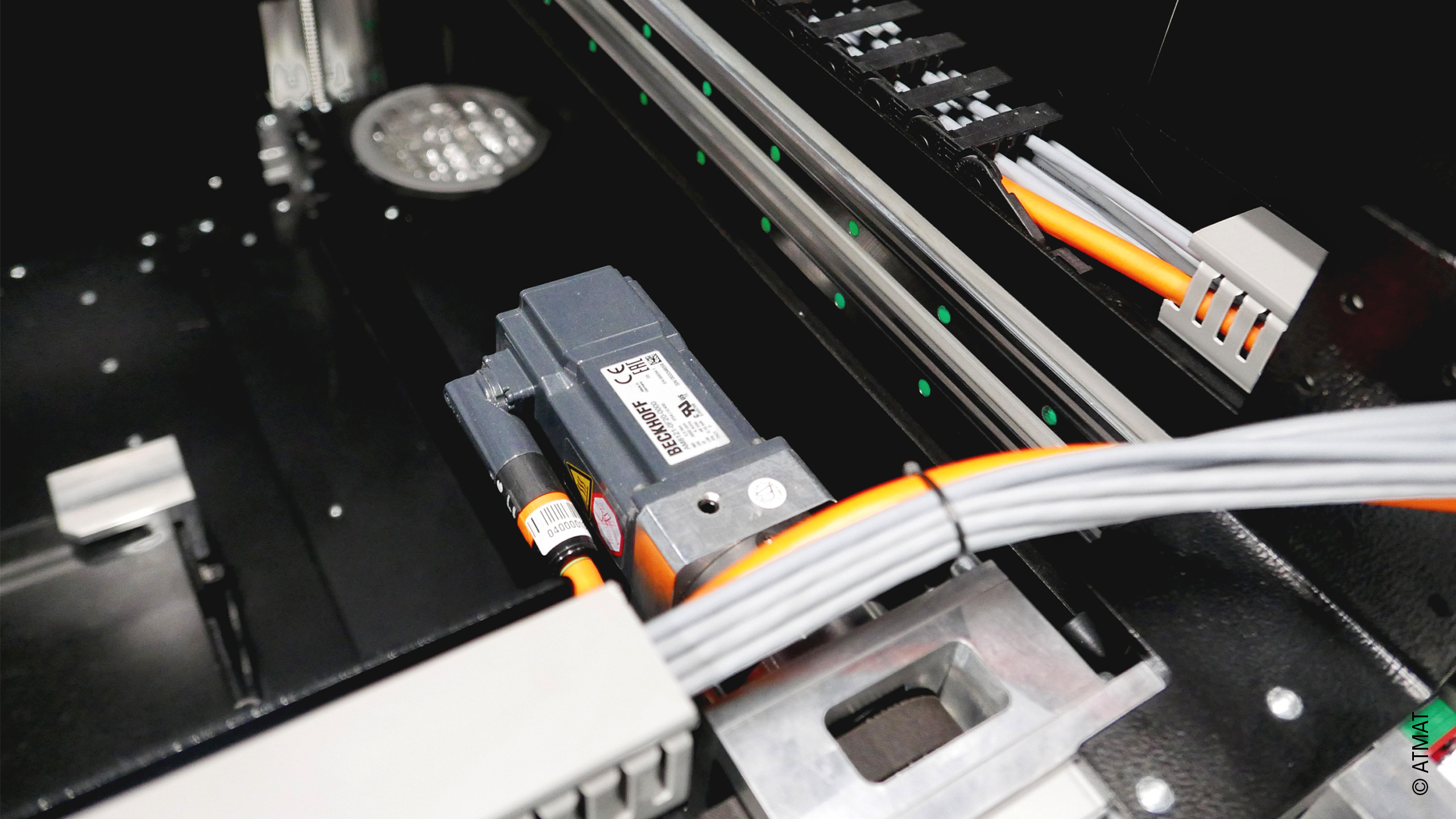
此外,汽车制造商正在认真思考将 3D 打印用于整车制造的可行性(不仅针对一些限定版车辆,而且还可用于制作功能原型),以便能够在开始批量生产之前,以全尺寸 1:1 的比例展示新车型的真实外观。这种趋势不仅体现在汽车行业。“异常订单和小批量生产订单份额的增长很好地说明了这一点。”Robert Grolik 指出。这是因为 3D 打印不仅能够在正式生产前测试创新的解决方案;3D 打印也简化了公司小批量生产的组织工作。人们不再需要提前订购和储备零部件,只需根据具体的需求进行打印即可。
Saturn 大幅面打印机就是能够带来这些好处的典型产品。该设备专为复杂(即高精度)应用而开发,它有一个巨大的大理石工作台、一根龙门轴以及两个打印单元(主打印头和辅助打印头),可以实现高速打印。主打印头由两个挤出机组成,可以配备一到两个打印喷头。这样可以显著加快打印速度,即使是打印复杂的几何形状。巨型工作台中内置的四区加热系统可以保障工作平台的正确温度。其独立的温度控制不仅能够降低能耗,而且还能够更快达到设定的工作温度。巨型打印区域安装在一个带隔热的加热室中,以保持温度恒定。
紧凑型驱动技术助力实现高精度运动控制
ATMAT 为大幅面打印机配备了倍福的 AM8121 紧凑型伺服电机。它们与巨大的结构体一起,确保 50 μm(X/Y 轴)和 10 μm(Z 轴)的定位精度。对于 ATMAT 来说,以前使用 Jupiter 系列积累的积极经验对选择驱动产品起了决定性作用。“AM8121紧凑型伺服电机的其中一个优势是,它们可以通过 EL72xx 伺服电机端子模块驱动。”倍福区域销售经理 Krzysztof Pulut 说道。“由于标准 EtherCAT 端子模块的体积非常小,与传统的伺服驱动器相比,它们可以节省控制柜中的大量空间。此外,单电缆技术(OCT)将动力和反馈系统整合在一根电缆上,大大减少了打印机的布线工作。OCT 不仅能够减少布线出错的风险,而且还能够减少设备制造商需要保留的系统组件数量。”Z 轴的运动通过一个由 EL7031 EtherCAT 端子模块驱动的步进电机执行。

倍福还提供了所有 I/O 模块,包括安全模块。安全要求通过 EL6900、EL1904 和 EL2904 TwinSAFE 端子模块实现。用于监测挤出机头、工作台和腔体温度的特殊传感器也使用了相应的 EtherCAT 端子模块。“温度调节对 FDM 打印机的熔融分层具有决定性意义,因为它能够确保打印件的质量。”Robert Grolik 在解释端子模块对打印过程的重要性时说道。ATMAT 的自动化专家们还想到了另一个对确保良好打印效果至关重要的解决方案:他们使用激光传感器测量打印头和工作台之间的距离,从而提高打印质量,尤其是在打印第一层材料时。
通过 TwinCAT HMI 进行直观操作
3D 打印机通过 TwinCAT 3 和适合控制柜安装的经济型面板型 PC CP6700 自动控制。“即使对于复杂的 3D 打印订单,Intel Atom® 处理器(双核)和 4 GB 内存也完全够用。”Robert Grolik 强调说道。在系统完整性保护方面,专家们使用 30 GB 的闪存作为外部存储介质,并配备了倍福的 1 秒钟 UPS。控制硬件能够在恶劣的生产条件下工作,并集成 TwinCAT HMI 可视化软件,这些都是选择倍福的决定性因素。“TwinCAT HMI 可视化软件提供多种布局,响应时间短,并支持远程访问和二维码扫描仪。”Robert Grolik 说道。
“倍福的开放创新坚定了我们与其合作的决心。倍福每年都坚持开发和实施新的解决方案,这在控制系统制造商中实属罕见。从我们的角度来看,最重要的还有 OCT、先进的 HMI 开发环境,以及安装 Windows 10 操作系统的面板型 PC,它们都有利于我们将 3D 打印机集成到更高级别的系统中。”