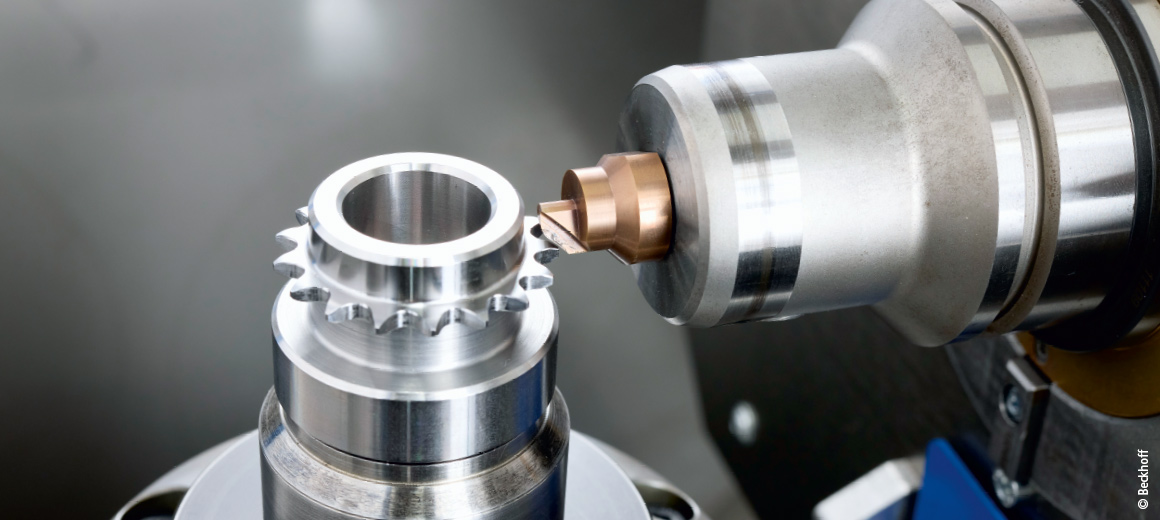
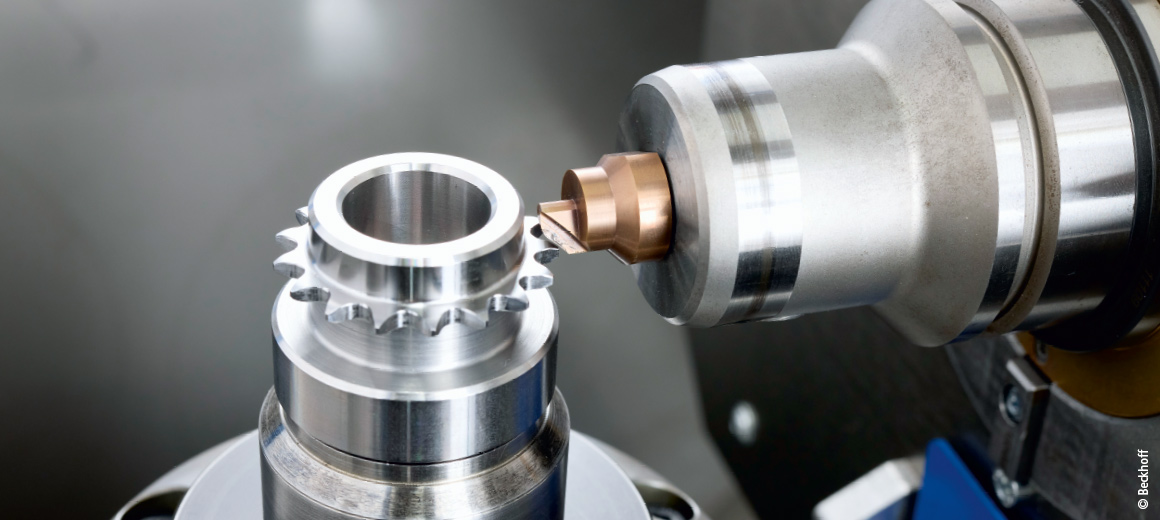
基于 PC 的控制技术助力实现齿轮自动倒角及去毛刺
德国黑森林地区是众多创新技术的发源地,其中就包括径向倒角技术。来自富特旺根的 Tec for Gears (TfG) 公司利用倍福的 TwinCAT PLC/NC PTP 和 EtherCAT 超采样端子模块等设备,成功地将过去高度依赖人工操作的生产流程转变为高度自动化的生产模式。通过技术革新,齿轮的倒角和去毛刺工艺在精度与可靠性方面有了质的飞跃,且速度也大幅提升,并且这一过程现在可以直接集成到生产流程中。
在倒角过程中,旋转切削刀具径向移动至旋转的齿轮表面,去除齿廓毛刺。其目的是在前齿边缘形成精确的倒角。“刀具沿着齿轮端面进行切削,将材料逐渐去除。”富特万根 Tec for Gears 公司创始人兼总经理 Niklas Müller 解释道。这一过程实现了部件的连续、无间断加工。这看似简单的需求背后,实则对加工过程中的控制技术提出了极高的要求。“仅仅是让两个以不同速度旋转的轴按照特定的旋转比精确实现同步,便已经是一项极具挑战性的任务。”倍福巴林根分公司的销售工程师 Dieter Völkle 说道。这是因为主轴的转速高达每分钟 17,000 转,而卡盘内夹持的工件也需以每分钟 1000 转的速度同步旋转。两个主轴的旋转比是依据工件与刀具各自的边界条件精心计算得出的。
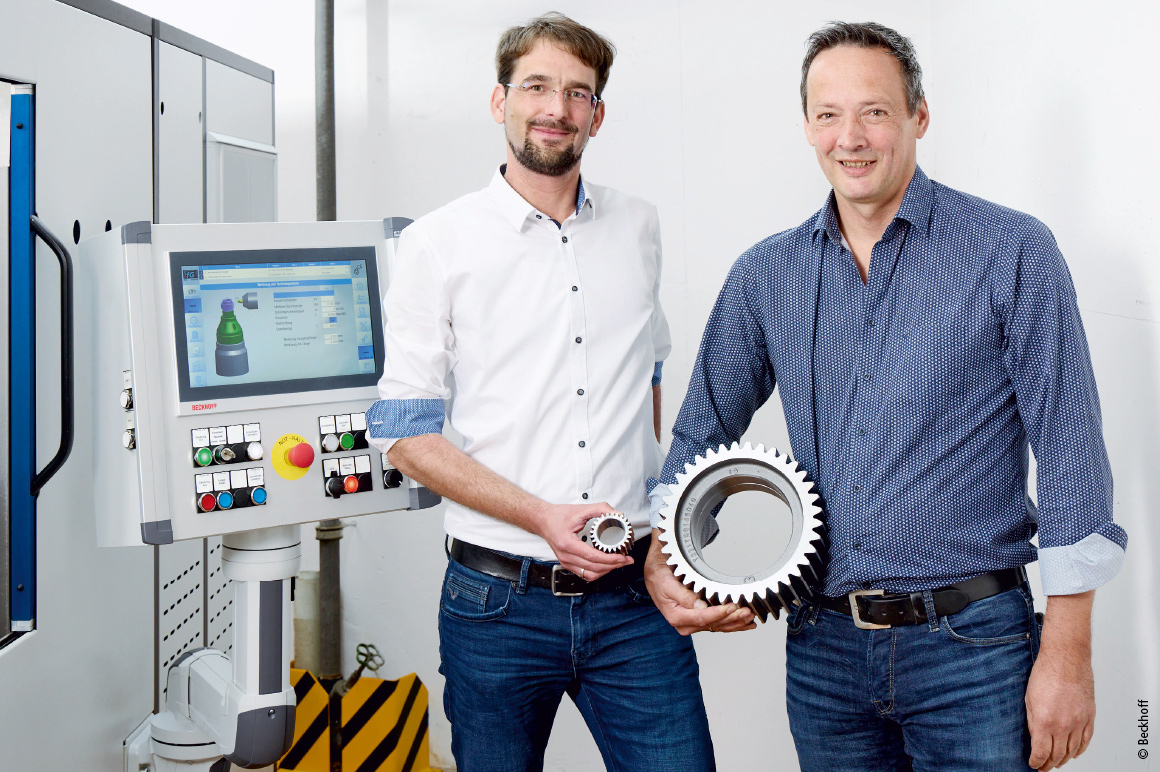
CNC 还是凸轮?
在项目的初期阶段,我们面临着诸多不确定性:CNC 系统是否为必需项?凸轮是否能满足需求?以及齿隙的检测速度需要达到多快? 最终,倒角机的独特需求通过 TwinCAT 3 PLC/NC PTP、TwinCAT 3 NC Camming 和 TwinCAT 3 Motion Control XFC 得到精准满足。这些软件组件与 TwinCAT HMI server 一起在搭载 Intel Atom® 四核处理器的高性能 CX5140 嵌入式控制器上运行。“自项目伊始,Dieter Völkle 便凭借其在系统设计领域的深厚专业知识,为我们提供了宝贵的支持与指导。”Niklas Müller 解释道。
由于齿轮在未对准位置的状态下被夹紧,因此在加工前必须确保切削刀具与齿隙之间精准对齐。不过,这一步骤并不会造成加工时间的明显延长。因此,对齿隙进行高速且精准的检测显得尤为重要。根据齿数(使用的接近开关为每个轮齿产生两个脉冲信号)的不同,系统会生成一个速度非常快的信号序列。为了精准记录这些高速信号,TfG 使用了具备多时间戳功能的 EtherCAT 端子模块 EL1258,实现了高达 100 kHz 的采样率,并通过多个时间戳将传感器脉冲传送到控制器中。这样就可以在确定轮齿的准确位置的同时,检验夹紧的产品。
除了旋转轴的编码器信号之外,用于补偿热膨胀的线性测量系统的数值也被整合到刀具的同步和定位中。刀具主轴与工件轴之间的同步必须保持高度稳定,即使在倒角作业中切削力增加,且主轴转速飙升至每分钟 17000 转的高速状态下,也需要保持这种稳定性。Tec for Gears 销售部的 Volker Eschle 评论道:“工件和切削刀具的持续高速旋转使我们的 RGC350 倒角机能够实现极短的加工周期,同时确保加工质量的稳定性。”TfG 通过倍福的高精度运动控制产品、AX5000 紧凑型伺服驱动器和 AM8000 伺服电机实现了加工过程中的极高重复精度。“我们的机床之所以能够达到如此高性能与高精度的自动化水平,得益于倍福先进的技术方案,这是任何其他控制制造商的技术难以企及的。”Niklas Müller 说道。
设备制造商要求齿轮“切边清晰”
如今,越来越多的设备制造商及其供应链合作伙伴对于齿面加工的要求愈发严苛,不仅追求精确无误、边缘清晰的倒角加工,而且要求在设计图纸中注明“倒角与轮廓完全契合”。传统的去毛刺方法虽能有效去除边缘的毛刺,但所留下的边缘依旧锋利,无法满足现代齿轮加工领域对边缘平滑度与精度的严格要求。径向倒角技术因此应运而生,成为解决这一行业痛点的关键。凭借自动上下料设计,RGC350 每年可完成一百万个零件的倒角处理。一般来讲,每个齿轮的加工时间为 8 到 10 秒,整个加工过程包括工件夹紧、齿隙检测、轴同步、倒角、脱夹。
机床可用于加工直径在 10 毫米到 300 毫米之间的几乎所有类型的齿轮,即使是双齿齿轮、多齿齿轮以及齿廓重叠干涉的齿轮也不在话下。它还具备加工螺旋齿轮传动部件的能力。在计算曲线时,也会综合考量另一个空间轴和耦合,以补偿螺旋角带来的影响。
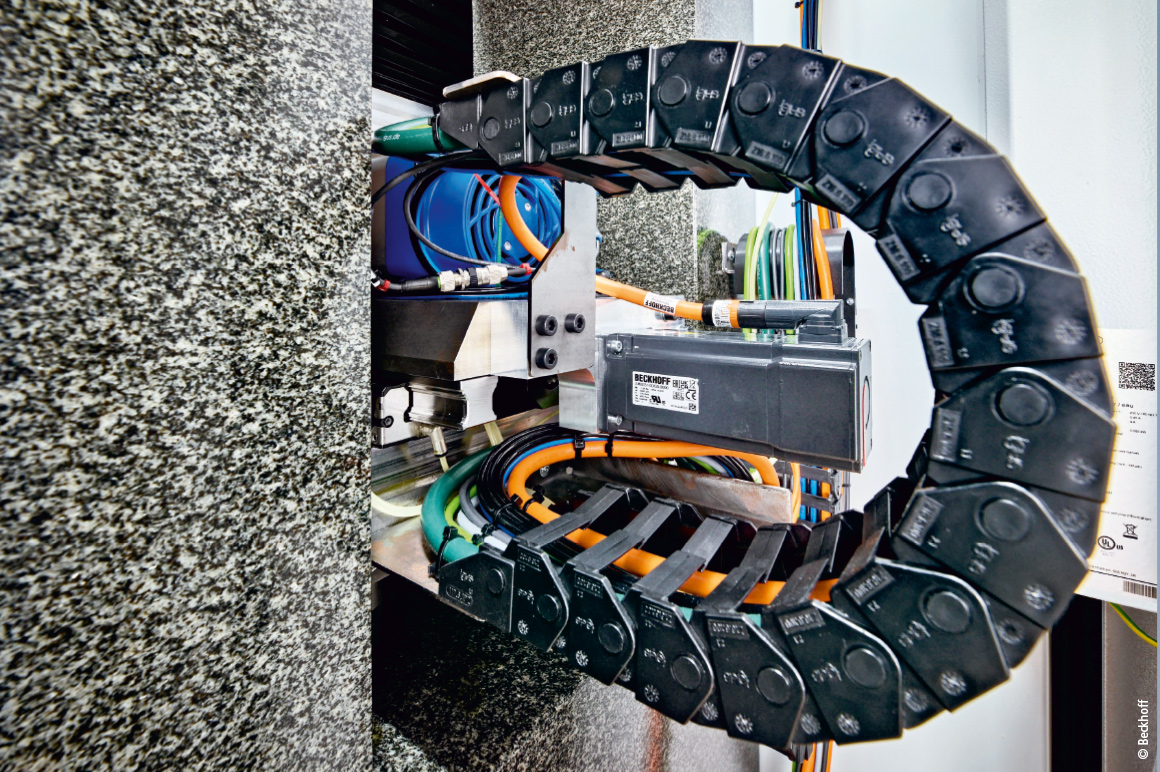
HMI 的直观操作诠释了复杂技术的繁琐实现过程
Niklas Müller 表示,尽管存在种类繁多的加工需求,机床操作人员却能在短短 10 分钟的时间内迅速完成机床的重新调整,以顺利安装新齿轮。“所有用于自动倒角作业所需的数据都通过 XML 导入到控制系统中。”Dieter Völkle 补充道。操作人员只需在 TwinCAT HMI 的可视化系统中调用与工作相关的数据集,然后夹紧相应的工具即可。这种简单的换装过程使得 RGC350 不仅适用于应对大批量生产的挑战,也适用于订单频繁变动和小批量定制需求的合同制造商。“我们的一个客户因此能够用一台机床替代了原本需要两班制操作的共计四个手工工作站,然后将员工安置到其他更具价值的岗位。”Volker Eschle 说道。
为了提高加工效率,大部分客户都选择将倒角机与自动进料和排料系统无缝集成至其生产流程中。基于 PC 的控制技术的高度灵活性和开放性在这类项目中得到了充分体现,该技术允许根据客户的具体需求进行调整。额外的驱动控制器和电机等扩展功能可以轻松快速地实施并集成到控制程序中。“这种前所未有的灵活性在帮助我们精准实现客户的构想的同时,也让我们自己的想法能够顺利落地,而这一切都是在不牺牲基本方案完整性的前提下完成的。”Niklas Müller 兴奋地说道。选择倍福作为控制技术合作伙伴的另一个原因是,一旦客户遇到任何问题或挑战,倍福都能迅速响应,不仅提供中肯的建议,而且以解决方案为核心,提供专业、高效的技术支持。
高效刀具管理
刀具管理是这个项目的另一个重要需求。这背后的原因在于,每个齿轮型号都需要与之相匹配的倒角刀具,以确保加工精度。因此,TfG 根据部件的具体尺寸在德国精心制造了这些刀具。鉴于工件的多样性与差异性,客户需面对庞大的刀具管理挑战,并在制定生产计划时充分考虑刀具的使用寿命。这有助于客户优化刀具的使用策略,避免由于刀具过度磨损而生产出不良工件。
目前,可以在 HMI 中为每个刀具创建刀具寿命计数器。通过可视化界面为每把刀具创建了唯一的序列号,机床调试人员便能根据订单的具体尺寸要求,灵活选择那些剩余使用寿命充足的刀具进行加工。“尽管部件更换频繁,但刀具无需经常更换。”Volker Eschle 说道。刀具与工件不匹配的情况往往容易导致发生碰撞,给客户带来不必要的麻烦和损失。“我们致力于在未来彻底消除这种混淆状况及可预见的错误,进一步优化刀具管理。”Niklas Müller 说道,“能够与倍福这样出色的系统合作伙伴携手,我们对未来的成功充满信心。”